Keeping your customer happy with carrier status notifications!
- Jun 26, 2019
- 3 min read
In this post I’ll describe how the process works to receive an inbound EDI 214 Carrier Status message and forward that on to the related customer. This scenario applies to any process where we have ordered product from our supplier and they ship directly to the customer. We then receive the parcel status notification from the carrier which in turn needs to be sent to the customer.
As an example we could cut a PO to a supplier and have them ship the product directly to the customer. In this case when they ship the product they would send us an EDI 856 (Advanced Ship Notice) which contains the related Carrier Tracking Number (CTN). We would then receive the EDI 214s from this carrier with the CTN as the unique identifier. If we have SLS (Service Level Shipping) enabled in ECC we could post these 214s against the related inbound delivery but most folks don’t use this functionality. Companies are often storing these EDI 214 messages in SAP Event Management to allow visibility to the shipment handled by the carrier.
Now let’s go through how we can go about processing this inbound EDI 214 and turn it around and send it to the customer.
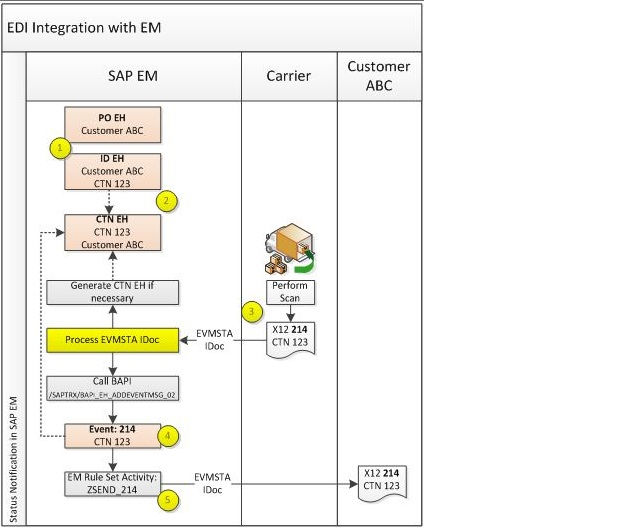
Using the process flow diagram above as a reference:
Create a Purchase Order (PO) for a particular product and have the ship to address reflect your direct customer (Customer ABC). I.e. The supplier will be responsible for shipping the goods on the PO to the customer directly. - The corresponding Event Handler (EH) is generated in SAP Event Management (EM) for the Purchase Order Line in order to provide visibility to the PO process at an item level - The supplier processes the order and prepares the goods for shipment - The supplier issues the goods to the carrier and obtains a Carrier Tracking Number (CTN 123) from the carrier - The supplier then sends us an Advanced Ship Notice (ASN EDI 856) telling us that the goods have been shipped and provides the CTN. - In SAP ECC we would take that ASN and create an Inbound Delivery, against the PO, storing the CTN (We would also typically turn this inbound delivery around and send a corresponding 856 to our customer ABC so that they are aware the product has shipped and giving them the carrier tracking number as well - This Inbound Delivery would generate the corresponding EH at the line level, in SAP EM, in order to provide visibility to the Inbound Delivery. This EH would carry the CTN and Customer ABC detail as parameters
In the EH Update activity for the creation of the Inbound Delivery EH we would create a custom activity to create the corresponding CTN EH if it does not already exist (In the event the 214 arrives prior to the 856 ASN) - If the CTN EH already existed at the time of Inbound Delivery EH create then send an event to update the CTN EH with the Customer ABC parameter - The CTN EH would contain the Customer ABC as a parameter - The Tracking ID would be the CTN 123
The carrier, having picked up the package, performs their scans as the parcel / package proceeds through their transportation process - Each relevant scan is sent, via an EDI 214 message, to us where we translate it in to an EVMSTA IDoc - The EVMSTA IDoc is then processed in SAP EM using the standard inbound IDoc processing function module - Using the event EH generation functionality we would write custom code to check to see if a CTN EH already exists and if one does not exist then to go ahead and create it
The IDoc processing calls function module /SAPTRX/BAPI_EH_ADDEVENTMSG_02 to create the event in SAP EM - This event has tracking ID CTN 123 and will be listed and processed against the CTN EH - Rule set activities are used to process the 214 event
A custom rule set activity needs to be created in order to do the following: - Find the associated EVMSTA IDoc to the message being processed - Copy the IDoc data and generate a new outbound EVMSTA IDoc for partner ABC (Parameter on the CTN EH) - The EVMSTA IDoc is then mapped in to an outbound 214 and sent to the customer
That’s pretty much all there is to the story. You can certainly leverage SAP EM to automate some of the key EDI processes in order to increase customer satisfaction.
Comments