SAP Track and Trace - Inbound Logistics
- Jun 30, 2019
- 6 min read
In the last article on SAP Track and Trace I discussed the Outbound Logistics scenario. In this article, I will discus how we can provide full visibility into the inbound logistics process by leveraging SAP’s Event Management module and EDI carrier status notifications. Organizations that place purchase orders (PO) for their suppliers or manufacturers have a very real need to make sure that the product arrives at the intended destination on the date that it was requested and promised. Scheduling receiving resources and ability to meet customer demand, all rely on the product getting to the warehouse when it was scheduled to be there.
Do you have enough time between when you find out about the issue and the time needed to correct it?
Do these issues in inbound logistics cause disruption and potentially lead to lost customers and sales?
The key to remedying this issue was discussed back in the 1990s and termed “Supply Chain Event Management” – give me the ability to monitor the events occurring throughout my supply chain, as and when they occur; let me measure these events against what I had expected to occur, and if it differs in any way, let me know so that I can take proactive measures to correct it. SAP was a part of the “think tank” that coined the term “Supply Chain Event Management” and created the product SAP Event Management to provide this Track and Trace functionality.
Inbound Logistics
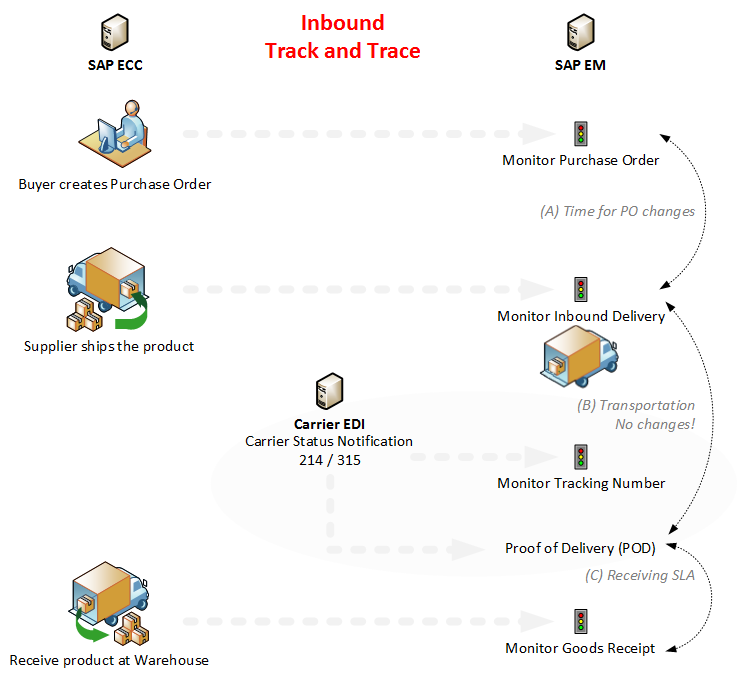
With regard to the above diagram, let’s discuss the inbound logistics process in detail. A buyer creates a PO to match a demand for more product. On saving the purchase order, an event handler (EH) is created in SAP Event Management (EM) in order to track the purchase order’s status. From that point on, any changes to the purchase order are accordingly reflected against the SAP EM Purchase Order EH so that anyone monitoring the purchase order will also receive those updates. A typical change that is monitored against the PO, at this stage, is the PO confirmation. For example, has the PO confirmation been received? Did the date change? Did the quantity change? Did the price change?
Once the PO is confirmed and the supplier actually ships the product, the supplier sends an Advanced Shipment Notification (ASN) to let us know the details of the shipment. In SAP, the ASN relates to an inbound delivery against the PO. At this time, an EH is created in SAP EM in order to track the inbound delivery’s status. Note that the SAP EM inbound delivery EH and the PO EH are linked with each other, much like the two documents are linked via the confirmation control area of the PO in SAP ECC. The inbound delivery was assigned a tracking number/s just prior to the vendor shipping the product. The tracking number is used to create a tracking number EH in SAP EM in order to monitor the tracking number status going forward. Note that the tracking number EH is linked to the inbound delivery EH, allowing for complete upward and downward navigation from any of the applicable documents (purchase order, inbound delivery, tracking number).
Once the carrier makes the first scan against that tracking number/s (pickup from the suppliers location), we will receive a notification from them stating that this event had occurred. Carriers typically provide an EDI X12 214 carrier status notification message to give this detail. When we get the 214 message, we typically use a translation tool (e.g. SAP NW PI) to convert it into an EVMSTA IDoc and have it posted to SAP EM. Each 214 message is posted against the corresponding tracking number EH as an event, and the status is updated accordingly at the time of posting.
Depending on the status (e.g. Proof of Delivery (POD)), we may choose to automatically flow the event to the related event handlers. For example, a POD posted to the tracking number EH informs us that the package was delivered. That tracking number is also on the inbound delivery, so we could flow the POD event to the inbound delivery EH and could adjust the status to “Arrived at the DC (distribution center).” In addition, the inbound delivery is associated with a PO so we could adjust the PO’s shipment status to “Arrived at the DC.” This gives the DC receiving team visibility into the fact that we have product waiting at the warehouse to be received. In addition, it gives visibility to the procurement and sales team to know that the goods have arrived but have yet to be received.
Another key example of a pertinent carrier status event would be one where the Estimated Time of Arrival (ETA) date / time has been adjusted. We would need to flow that onto the carrier tracking number EH, inbound delivery EH and the PO EH because all partners in the extended supply chain need to be aware of the change in delivery date. In addition, the inbound delivery EH needs to send the new date to SAP ECC and update the inbound delivery with the new date, which allows the warehouse receiving team to adjust their expectations accordingly around when they will be receiving this PO.
An adjustment in timing during the current execution of a process can lead to the realignment of the plan for future steps in the plan. Issues are addressed as and when they are first detected. This helps in the minimizing the impact of “missing” a milestone in your supply chain plan.
Once the goods have arrived, we follow a standard goods receipt (GR) process to move the goods into unrestricted stock, allowing them to be assigned to the waiting demand elements. On GR, an event is sent to SAP EM to post against the inbound delivery EH in order to change the status to “Goods Received.” The GR event is also posted to the PO to let the buyers know the status of the PO is “Fully Received” (unless this was one of many shipments in which case it was partially received).
Note: By capturing the events for “Carrier POD” and “Goods Receipt,” we are able to report on how well the DC is performing their receiving function. Is receiving performing according to the agreed SLA to receive product into the warehouse? As you can see, we can get full visibility for the supply chain members from the purchase order, through inbound delivery, carrier status notifications and GR. The standard procurement Visibility Process provided as a template in SAP EM also includes the Vendor Invoice receipt and payment so true, end-to-end Procure-to-Pay visibility of status and exceptions is possible.
Value-Added Components
Suggested value-adds to the process would include:
Create an expected event for “pickup” on the inbound delivery EH: The pickup event would be used to ensure that we actually get an event for this tracking number, otherwise we have “lost” a tracking number somewhere. We would need to discuss with our vendor why we did not receive a carrier notification for that shipment.
Create an expected event for “delivered” on the inbound delivery EH: The delivered event has the promised delivery date and can be used to check whether the carrier and supplier are executing according to the plan. If the Delivered event goes overdue without being received, then the DC can be warned that the delivery is running late.
The PO process is often used together with EDI / IDoc postings. If these IDocs fail, there is the potential to capture these against the corresponding PO to provide further visibility to a potential issue. For example, an inbound ORDRSP IDoc failure implies that the supplier’s order confirmation (EDI X12 855) has not posted against the PO. It could mean that a price, date or quantity change could be missing for the PO. If this situation persists, then the remaining steps in the procure-to-pay process will also experience issues as the documents will be out of sync. As long as the PO is correctly specified on the ORDRSP IDoc, an event can be sent to the SAP EM PO EH on an IDoc posting failure. This event would change the PO status to “PO Confirmation Failure” and potentially send an alert to the buyer to prompt the correction of the error.
PO output is sometimes not trusted to have been generated. The PO output is the technique used to send the PO content to the supplier. This output can be sent via email or EDI (among others). An event could be sent to the SAP EM PO EH to let it know that output was successfully created. It opens up the functionality for responding when output is not generated for a PO in a timely fashion. This is key to know because it ensures that each and every PO gets to the supplier as needed.
Implementing Process Track and Trace There are several factors to consider when planning to implement a track-and-trace solution when using SAP EM combined with EDI:
The supplier must be able to provide a good tracking number per carton as well as the used carrier.
The carrier must have the ability to electronically tell us about the status of a tracking number for our shipments even though the shipment is planned by our supplier on our behalf.
Purchase order, inbound delivery and tracking numbers need to be tracked in SAP EM: Stick as close to a standard implementation as possible.
Plan your SAP Track and Trace solution with reporting and analytics in mind.
Be sure to accommodate for “re-evaluating” of expected events in your design.
If you are considering enabling pro-active alert notifications for exception messages, then ensure that your baseline master data driving these alerts is of a very high standard. In addition, make sure that your supplier’s data is mature and correct according to the shipment, otherwise you will be spammed.
Please feel free to leave any comments.
Comments